- Optimizing Operations
- blog
Item picking vs. case picking order fulfillment
Find out more about the difference between item picking and case picking order fulfillment and the available automation solution.
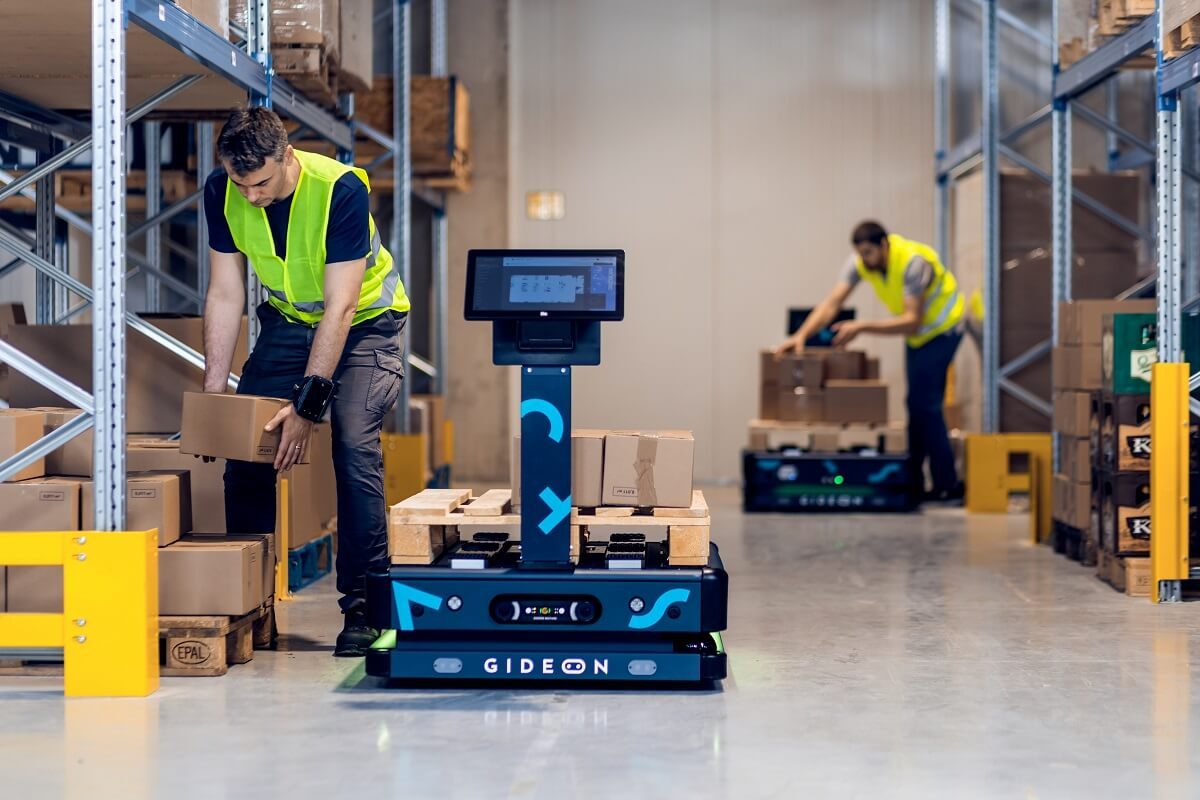
/