- Optimizing Operations
- blog
Seven signs you need (more) warehouse automation
Recognizing the right time to automate will help you get the most out of the new technologies and get ahead of the innovation curve.
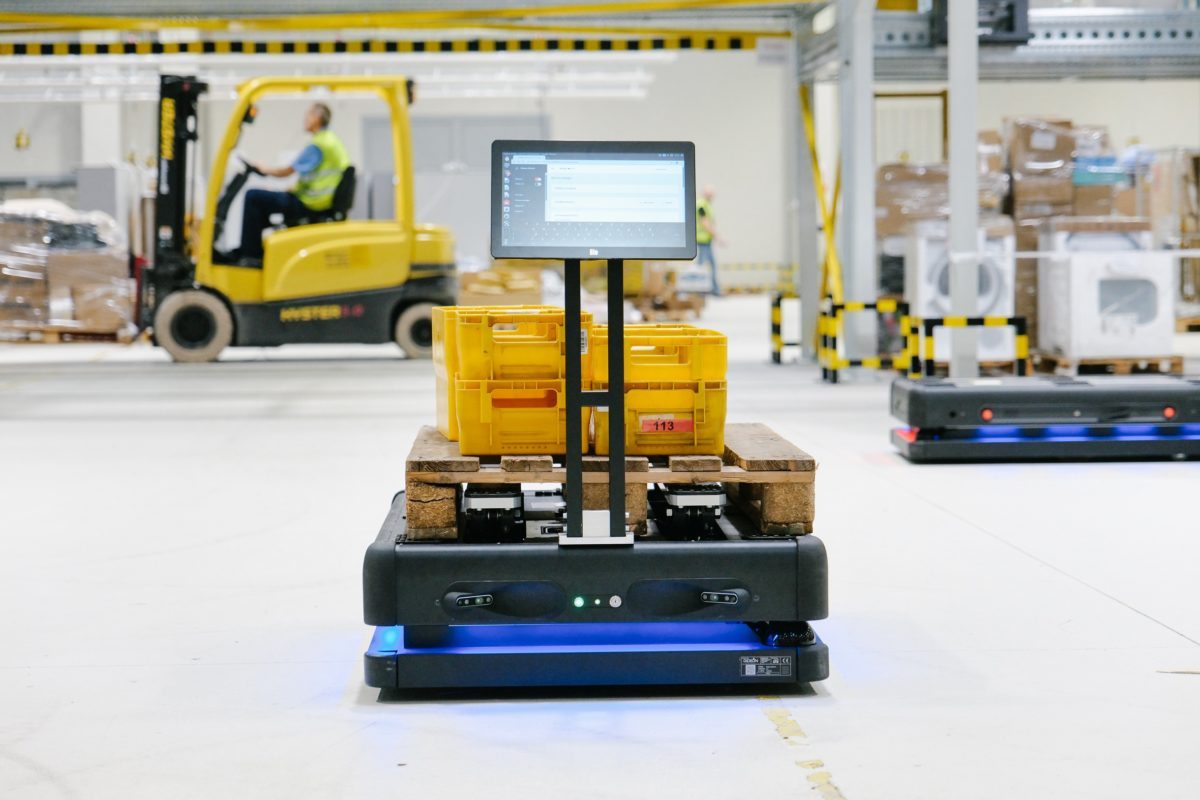
/