- Optimizing Operations
- blog
Discover how warehouse automation increases productivity
Discover how automation and robot-assisted order picking can help you optimize your day-to-day operations and manage labor shortages.
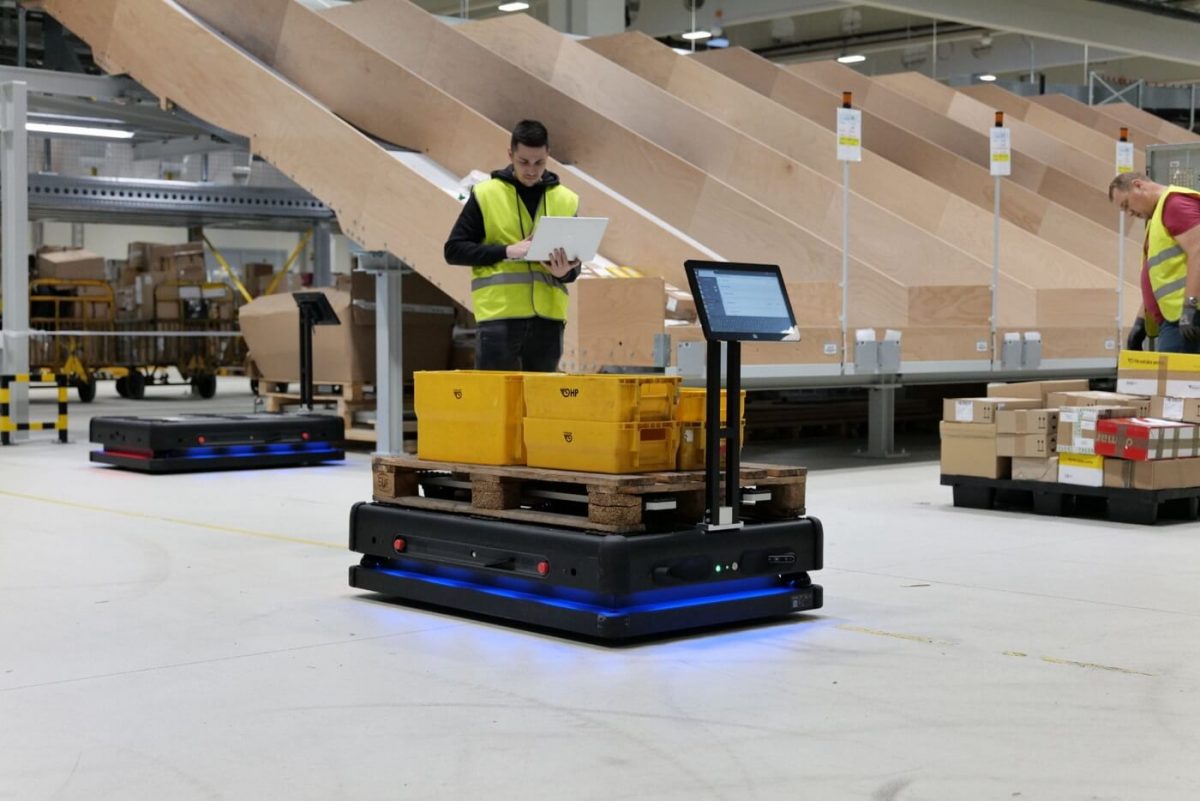
/