- blog
3D depth sensing for robots 101
Check out our overview of 3D depth-sensing technologies that allow mobile robots to perceive the world around them.
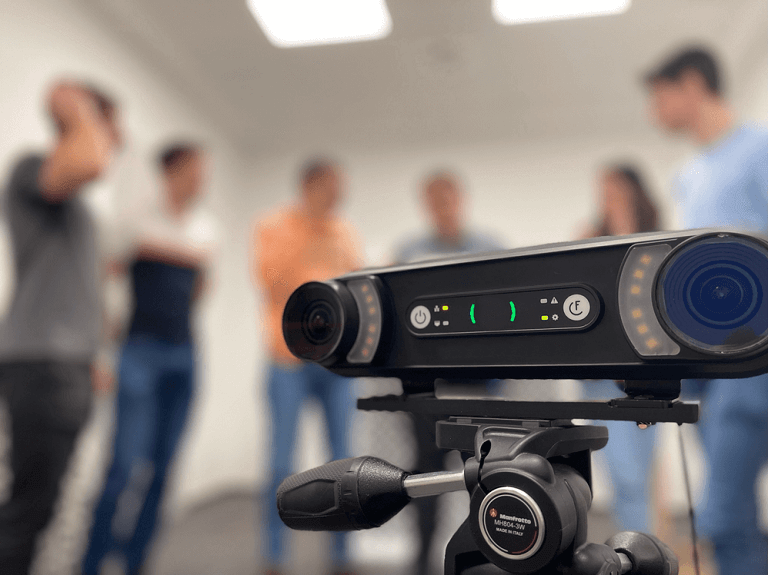
/